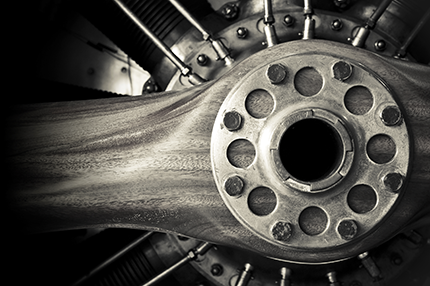
Present and future of aviation titanium fasteners market
Whether military or civilian, modern aircraft mechanical connection method uses a lot of fasteners will be composed of the aircraft parts, components, parts integrally connected, fasteners less then hundreds of thousands, as many as a million pieces, its type structure varied, to be based on the use of the site, the environment, the use of load, life requirements, different methods of installation performed selection.
There are a variety of aerospace fasteners Category: Removable or not divided by removable fasteners and permanent fasteners, which include removable fastener bolts, screws and nuts, the permanent lock bolt fasteners including high / High-locking nuts, conventional rivets Central trough rivets, blind rivets, inserts and the like; or not by easy installation into open structure using fasteners and fastener do not use open architecture; load divided by force a tensile shear type fasteners and fastener; can be divided according to the assembly precision fasteners and interference-gap type fasteners. Aerospace fasteners are classified by product type is more common, can be divided into: rivets, bolts (screws), Nuts, single fasteners, specialty fasteners and other types of products, each category includes a plurality varieties, specifications, to meet the different materials, installation requires structure.
Aerospace fastener market situation
World famous Company Profile
The world aerospace fasteners mainly from the United States, Alcoa (Alcoa), the United States casting (SPS), France Rees Space Group (Lisi Hi-shear), the United States Boeing (Boeing), the world’s larger companies tightening Monogram firmware and the US companies highly specialized companies monopolized and Russia aerospace fastener is self-contained for its domestic use. Every fastener company has its good products, and the majority of products for several companies cover each other, thus constituting aerospace fasteners supply network to meet the needs of the major aircraft manufacturers.
Alcoa Inc. is the United States in recent years by a number of companies engaged aerospace fastener manufacturing companies from integration, its main product (Table 1) include aluminum, steel, corrosion resistant steel, heat-resistant alloys, titanium metric and imperial bolts / screws, nuts, blind fasteners alloys and other superalloys and other materials, quick release fasteners, inserts and piston ring groove nail fastening systems, bolt fastening systems, special rivets, etc. .
American SPS company, most of its main products and Alcoa, the same or similar, including bolts, nuts, blind fasteners, inserts and plunger, quick release fasteners, including bolts and nuts products, including Cone bolts, adjustable diameter bolts, earless Nuts, non-metallic insert locknuts, with its high-strength and super-heat-resistant alloy bolts and nuts are more advantages.
France Lisi Hi-shear company whose main products include a variety of materials of high lock bolt / high lock nut system, high torque bolt, high shear rivets, rivet-sided / bolts and fasteners coatings.
Monogram US company, is a relatively strong professional company, whose main products include blind fasteners, adjustable diameter fasteners and temporary fasteners, wherein the composite structure with single threaded screw pump technology in the world. the strongest.
Advanced aerospace fasteners
Modern aerospace fasteners used materials include aluminum, carbon and alloy steel, stainless steel, titanium, heat-resistant alloys. Since titanium alloys have better overall excellent performance, thus more than 90% of threaded fasteners are titanium fasteners, including Ti-6Al-4V fastener majority, the main products include titanium screws, titanium High lock bolts, titanium screw pumping nails, nails and other titanium ring groove; fasteners engine used mostly for heat-resistant alloy fasteners; combination type fasteners such as nails, etc. Depending on the pumping structure using aluminum, stainless steel , a single material alloy, heat-resistant alloys, etc., or a combination of a variety of materials.
Aircraft structure, a large amount of fasteners, wherein the amount of certain species can reach hundreds of thousands, for airframe structural fasteners products mainly include rivets, threaded fasteners, single-sided fastening members as well as some special requirements fasteners. Which mainly comprises a fastener rivets and rivet head headless rivet, most aluminum structure using rivets from aluminum alloy, in order to meet the requirements of aircraft long life connection, there are head aluminum rivet head and compensation mostly by coronal head shape, At the same time high performance, such as high shear rivets rivets are also used in aluminum alloy structure in order to meet the needs of the respective structural strength, in addition, more advanced composite structures including titanium, niobium rivets rivets, bimetal rivets; bolts fastening members include ordinary bolt, lock bolt and cone bolt high, matching nut including ordinary nut, self-locking nuts, high-locking nut, Nuts, and so on; do not use open-sided fastener structure, the main form of structure Drawing type pumping nails, nails and other screw pump; special fasteners include quick release fasteners, ring groove fasteners and composite fasteners.
Rivet Fasteners
Rivet fasteners Fasteners is one of the largest on the aircraft, which materials are aluminum, stainless steel, heat-resistant alloys, titanium, etc., most rivet is mainly used for aluminum, titanium, composites representing connecting thin structure with a diameter generally less Φ4mm, in order to meet the requirements of aircraft structural high life, mostly using automatic drilling and riveting machines and flexible assembly system assembly, with the continuous improvement of material strength rivets, developed a significant portion corresponding use The bearing rivets, such as double metal rivets (Figure 1) and high shear rivet (Figure 2), the strength of titanium alloy can achieve high intensity shear bolt lock.
Threaded Fasteners
Threaded Fasteners are carrying a larger part of the largest fasteners on aircraft, including ordinary bolt bolt, lock bolt high, cone bolts. For aircraft design, weight loss is an important indicator, high strength materials can achieve a low contrast intensity replace large-sized fasteners, so the airframe structure of extensive use of 1100MPa GR5 titanium fasteners (such as Fig. 3). In addition, to be considered in the design besides than the outer strength, we need to consider the anti-fatigue, corrosion resistance, rigidity, brittleness, compatibility, heat resistance and other properties.
ormal is a double-sided installation bolt fastener into tensile and shear-bolt bolt, the first type includes a variety of driving groove Shen head, hex head, cylinder head, twelve angle head, D type first class, which is mainly used for construction countersunk fastener surface having aerodynamic requirements; hexagonal head, twelve top corner tensile bolts used primarily in parts of the connection requirements, while according to the structure of the material is installed, connection status, temperature bolt nut material requirements and supporting the need for different surface treatments. In connection assembly aircraft, usually using self-locking nut bolt ancillary, it must be used in the assembly torque limiting wrench for installation, ordinary bolt mainly used removable structure, in a permanent connection structure, basically by other ordinary bolt instead of having to connect a variety of fastening systems overall performance.
High lock bolt / high lock nut fastening system is a double-sided installation for aircraft structures riveting single application of fastening systems, because of its many advantages, the plane has been widely adopted, with 100 ° countersunk head, Two flat head type; shear type and tensile stress state of two kinds; ordinary high lock bolt, lock bolt high resistance to fatigue and light three forms of high bolt lock structure, supporting high-locking nut nut including ordinary, self-aligning High-locking nuts and sealing high lock nuts. Hi-lite and other light which high locking bolt system (Figure 4) higher than normal weight lock bolt 15 percent, is currently a large number of advanced aircraft; Eddie bolt / nut fastening system (Figure 5 shown), which is structurally similar to the high locking bolt fastening system for composite structures and automated assembly.
Tapered bolt system (Figure 6) is a thick interlayer for aircraft structural parts of the assembly to improve the life of the fastening system, the fastener can solve straight bar sandwich structure is difficult to realize a large installation of a large interference problems, a uniform amount of interference and balanced range after the entire sandwich assembly stress distribution, thereby increasing the static load capacity and dynamic load capacity.
Nuts Fastener
Nuts and bolts supporting the use of fasteners, having a variety of structural forms to meet different occasions, including hexagonal nut, twelve corner nut, spline nut, Nuts, barrel nut, high-locking nuts, etc., most the self-locking nuts are used in the form of structure. includes ear Nuts, Nuts, earless, swimming and floating, Nuts, Nuts, etc., with a seal and not seal two kinds of sealed form, in which no Ear Nuts can improve the life of structures; hexagon nuts with greater usage on airplanes; bihexagonal nut using a large amount of the engine and high-strength bolts; high-locking nuts (Figure 8) and high lock bolt supporting the use of higher usage, including high shear type lock nuts lock nuts and two high tensile type, having a common high-locking nut, self-aligned high-locking nut, lock nut and seal high upsetting the system and other high-locking nuts structure.
Blind fastener
Aircraft not open parts of the use of fasteners are mainly two structural forms, can be demolished parts such as flaps, doors used parts Nuts / bolts and quick release fasteners, as well as a large number of permanent joints are used sided pumping nails. Among them, the draw nail can be divided into two categories: one is the pull-type pumping nail (Figure 9), with a single rivet and blind bolt to the other; one is a threaded screw pump, with a gap-type, interference type and main load-bearing structure type (Figure 10), one side of which foot threaded titanium screw pump is designed for assembly and design of composite structures, interference single screw pump screw fastening systems can improve sealing and anti-fatigue properties, high strength pumping screw fastening systems can be used for primary load-bearing structure.
Special fasteners including nails and ring groove ring groove nail fastening systems, quick-release lock type fasteners and composite materials fasteners. Ring groove nails and nail ring groove fastening system is a double-sided single application to install permanent fasteners riveting, widely used in the Boeing and Airbus aircraft, with the form can be divided according to type and interferometric gap ; according to the installation can be divided into type and upsetting rivet riveting type. Currently most of the use of titanium alloys under load even ring groove nail fastening systems, such as titanium ring groove nail and nail ring groove fastening system (Figure 11).
Quick-release lock type fasteners (see Figure 12) it is mainly used to connect the flap and the doors of the site, with a variety of structural forms, enabling fast loading and unloading function, high reliability requirements, the need to meet up to 1,500 reliable demolition of the indicator.
Composite fasteners (Figure 13) is made of composite material fasteners, including rivets, bolts, screws and nuts, it is ideal for solving weight, strength, corrosion, lightning, radar images and other issues fasteners, now its intensity can reach high-strength aluminum rivets shear strength, can only be used in aircraft sub-bearing structure.
Future aerospace fasteners
Aerospace fasteners have large stand-alone use, variety and complex requirements and high, it has developed into a large product system, in order to meet higher performance requirements of the aircraft, the future of aerospace fasteners are the following trends:
- On the basis of current on fasteners and fastening systems, improve, improve its performance and functionality;
- further weight loss, can be controlled using the higher cost of strong materials, such as super-high-strength alloy material, can further reduce the volume and weight of fasteners;
- Vigorously develop automated assembly fastening systems, increased automation riveting coefficient;
- the ability to develop environmental sensors intelligent fasteners, in order to achieve a convenient remote control assembly and disassembly, and the timely achievement of various fastening and other related state perceived. (end) (End)